In today's fast-paced and interconnected world, effective supply chain and logistics management is crucial for the success of any organization. From ensuring timely delivery of goods to optimizing routes and managing inventory, businesses face a myriad of challenges that require innovative solutions. This page provides real-world examples of supply chain and logistics challenges that our students address through class and industry projects.
Supply chain engineers design and synchronize the networks and processes that move raw materials and supplies into production facilities, transform them into finished goods, and distribute products to customer markets. Supply chains are critical systems that enable industrial organizations to thrive.
Logistics
Optimizing Grain Shipments from U.S. Warehouses to Eastern Europe
Background: The U.S. has a surplus of grain stored in various warehouses across the country. For example: St. Paul: 100,000 tons, Kansas City: 150,000 tons, Denver: 95,000 tons, etc. Meanwhile, significant demand exists for this grain in Eastern Europe, with various regions requiring specific amounts of grain, such as: Sarajevo: 75,000 tons, Ukraine: 150,000 tons, Poland: 120,000 tons. Shipping costs per ton from each warehouse to each demand location have been estimated by the government.
The Challenge: Determine the cheapest way to ship the available surplus grain to meet the demand in Eastern Europe. Key factors to consider include the supply at each warehouse, demand at each destination, and the associated shipping costs.
1) Optimizing Shipments with Sufficient Grain Supply: Assuming there is enough grain to meet the total demand, the company needs to find the most cost-effective distribution plan. For example: The demand for Ukraine could be satisfied by shipping all available grain from St. Paul (100,000 tons) plus 50,000 tons from Kansas City. The remaining 75,000 tons from Kansas City could be sent to Sarajevo, and 25,000 tons from Kansas City could be sent to Poland. The objective is to identify the best combination of shipments to minimize total shipping costs, considering both the distances and per-ton shipping costs.
2) Handling Insufficient Supply: If the available grain is not enough to satisfy the full demand across all locations, some areas will receive less than their requested amount. In such a case, the challenge is to 1) Prioritize shipments based on factors such as urgency of need, economic importance of the region, or political agreements. Determine an approach that minimizes the shortfall while optimizing the cost of shipping the available grain.
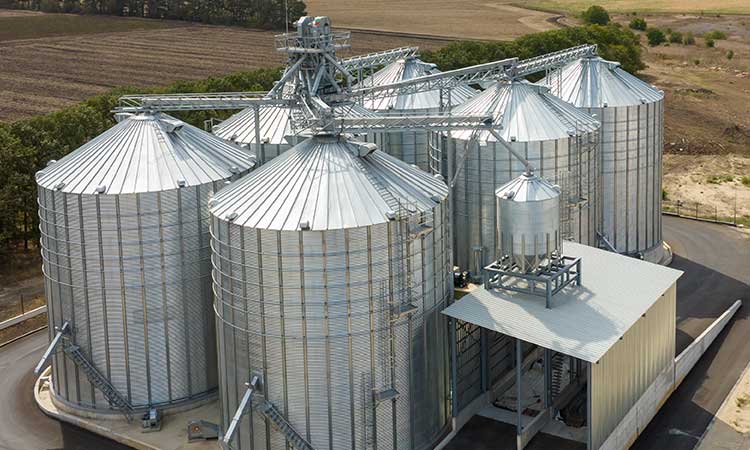
Manufacturing
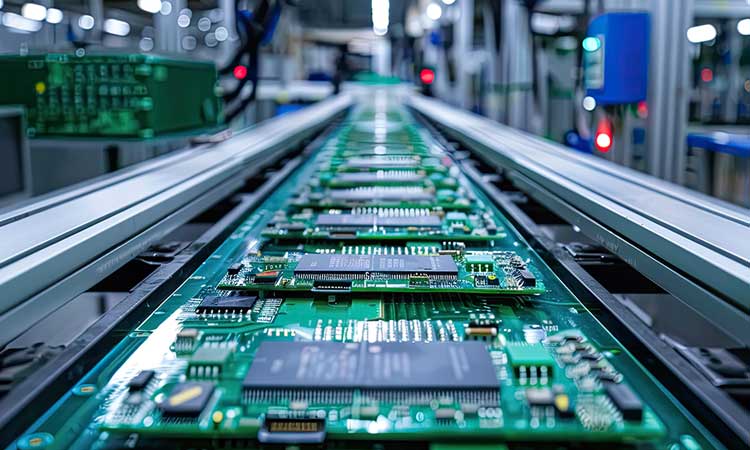
Manufacturing and Production Flow Line Challenge: Optimizing Cycle Time and Throughput
Background: A production line for circuit boards consists of four workstations in series. Each workstation performs a specific operation, and the time required for each operation varies. The production flow is as follows:
Workstation 1: Screen-Printing - The first workstation is a screen-printing operation that takes 30 seconds per board.
Workstation 2: Component Placement - The second workstation has three placement machines running in parallel. Each machine takes 1 minute and 45 seconds (105 seconds) per board to place components.
Workstation 3: Reflow Oven - The third workstation is a reflow oven, which takes 38 seconds per board.
Workstation 4: Inspection - The final workstation has two parallel inspection devices, each taking 66 seconds per board.
The Challenge: To understand the cycle time (CT) and throughput (TH) for different levels of work in process (WIP) between 1 and 15. Additionally, we want to identify the critical WIP, which is the smallest WIP level that achieves the maximum throughput, and analyze the formal relationship between WIP, CT, and TH.
Key Definitions: Cycle Time (CT): The average time it takes a board to progress through the entire line. Work in Process (WIP): The number of boards that are between the start and end of the production line at any given time. Throughput (TH): The average number of boards produced per minute.
Cutting Stock
Your small company uses custom-cut steel reinforcing rod for construction jobs in metro Atlanta. These rods are purchased from a steel products distributor who is willing to cut the rods for you to specification.
However, the distributor cuts pieces from stock that is only available in fixed 60-foot lengths. That is, if you need two lengths of rod, one of 15 feet and the other of 45 feet, then a single 60-foot piece is cut in the obvious way with nothing left over (and all is well). On the other hand, if you need eight 7-foot pieces, then the 4 feet left over from the 60-foot original is yours to pay for as well. Of course, some of these excess pieces may be useful later, but you will have to find storage areas for such pieces which, in turn, costs something too. Indeed, what is left over may be useless altogether and is simply counted as scrap.
Thus, we would like to minimize the number of full 60-foot units/rods that have to be used in cutting all of the given lengths, which means that we may have to be reasonably clever in how we specify the pattern of cuts on each. For example, suppose you need to place an order for 10 pieces of rod having lengths 41, 24, 24, 22, 21, 19, 9, 7, 7 and 6 feet respectively. Since the total length of the 10 pieces is 180 feet, it is obvious that the best we could hope to use is three of the 60-foot spans, but is this even possible?
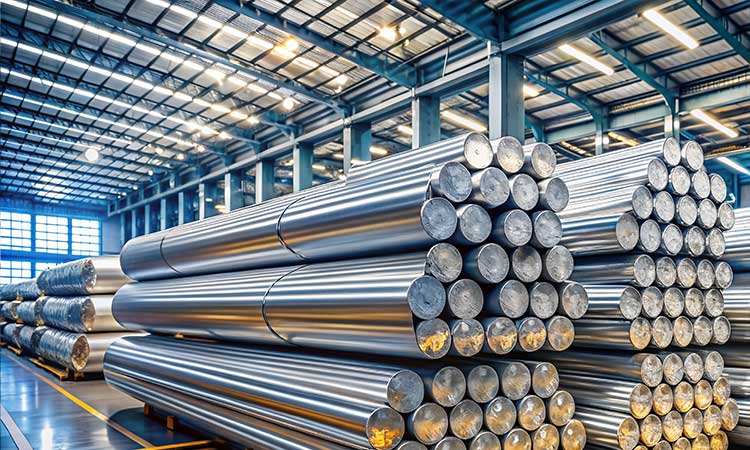
Naturally, this small numerical example is just a "toy" version of what might be a fairly messy problem in general. Indeed, in a real-world setting, you might have an order for hundreds or thousands of pieces to be cut from stock. In addition, the latter might come in varying sizes as well. And yes, your problem might be "multidimensional". For example, you might seek cutting patterns for 2-dimensional figures from rectangular sheets of aluminum with the aim of minimizing wasted area. You might be operating in a 3-dimensional setting where the requirement is to find a best packing configuration of irregularly shaped boxes into large unit shipping containers employed by an express mail carrier. Regardless, the underlying theme for any of these packing problems is the same; so too, by the way, is their enormous difficulty.
Planning
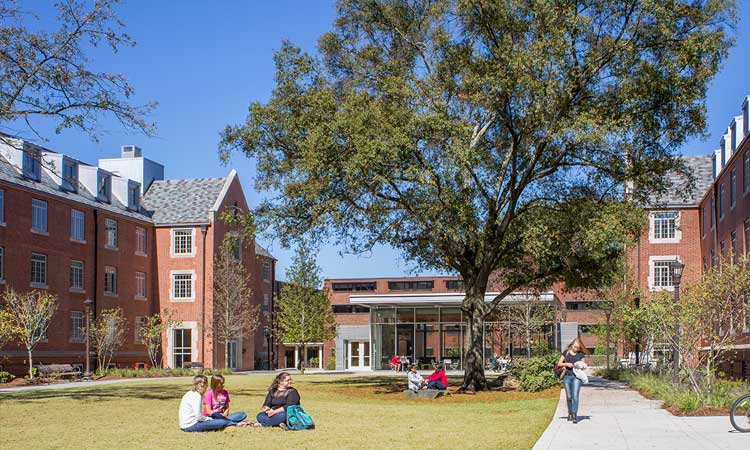
The Housing Office at Georgia Tech has to deal with a big problem every fall; how to make dormitory assignments so as to leave everybody reasonably happy. Of course, it may not be possible for everybody to be actually "happy" with their roommate assignment, so Housing's true aim would probably be to at least minimize the amount of misery created overall with the assignments.
Here's the thing...suppose that for Fall 2024, a total of 8251 freshmen are planning to live on campus in a dorm. Each student has, as part of their enrollment information, submitted a "wish list" regarding their preferences in terms of a roommate. These include such things as serious study habits, from Alabama, not from Alabama, likes jazz, talkative, no pet snakes, etc. Some of these attributes may have higher priorities than others, so Housing may "weight" them in some way.
In any event, what Housing would like to do is find a pairing of individuals that, in some sense, maximizes total "acceptability" and for which there is enough dorm space. For example, if two rooms are available for four students, but one student is absolutely unacceptable to the other three (under any circumstance), then two rooms will simply not suffice. Nonetheless, what do you think about the problem? Does it get easier or harder if rather than pairs, Housing is looking for groups of three (i.e. for dorms with 3-person suites)?
Scheduling
Optimizing Delivery Routes and Scheduling for a Retail Distribution Network
Background: A large retail company operates a distribution network that involves several warehouses, regional distribution centers, and retail stores. The company needs to deliver products from the warehouses to the retail stores in an efficient and timely manner. The company has a fleet of trucks, and each truck has limited capacity, specific delivery time windows, and assigned routes.
The Challenge: The company faces a logistical challenge in scheduling the deliveries to the retail stores. Specifically, they need to:
Schedule Deliveries Efficiently: There are multiple delivery destinations (e.g., regional retail stores) across a geographic area, each with specific delivery time windows (e.g., between 9:00 a.m. and 12:00 p.m., or 1:00 p.m. to 4:00 p.m.). Limited truck capacity means that some trucks can only carry a certain amount of goods, and the truck must be fully loaded to optimize fuel costs and delivery efficiency.
Minimize Delivery Costs: The company wants to minimize transportation costs by reducing fuel consumption and avoiding empty miles (miles driven without cargo or under-utilized capacity). Additionally, the company wants to minimize the number of trucks used to save on operating costs, but still meet all delivery deadlines.
Time-Window Constraints: Each retail store has specific delivery windows, which cannot be missed. If a delivery window is missed, it may result in penalties or lost sales. Some stores may have priority delivery schedules (e.g., large stores that need goods early in the day), while others are more flexible.
Dynamic Nature of Deliveries: Traffic conditions, weather, and other disruptions (e.g., accidents, road construction) can affect delivery schedules. The company needs to factor in uncertainty and be able to adjust the delivery plan in real-time. New orders may come in after the initial schedule is made, so the scheduling system should be adaptable and capable of quickly accommodating changes.
Seminar | Periods | Time |
---|---|---|
A | 2 | 9:00am - 10:00am |
B | 8 | 4:00pm - 5:00pm |
C | 4,5 | 11:00am - 2:00pm |
D | 1,2 | 8:00am - 10:00am |
E | 3,4,5 | 10:00am - 2:00pm |
F | 6 | 2:00pm - 3:00pm |
G | 7,8 | 3:00pm - 5:00pm |
H | 2,3 | 9:00am - 11:00am |
U | 1,2 | 8:00am - 10:00am |
J | 5 | 1:00pm - 2:00pm |
K | 6,7 | 2:00pm - 4:00pm |
L | 3,4 | 10:00am - 12:00am |
M | 8 | 4:00pm - 5:00pm |
N | 2,3,4 | 9:00am - 12:00am |
Warehousing
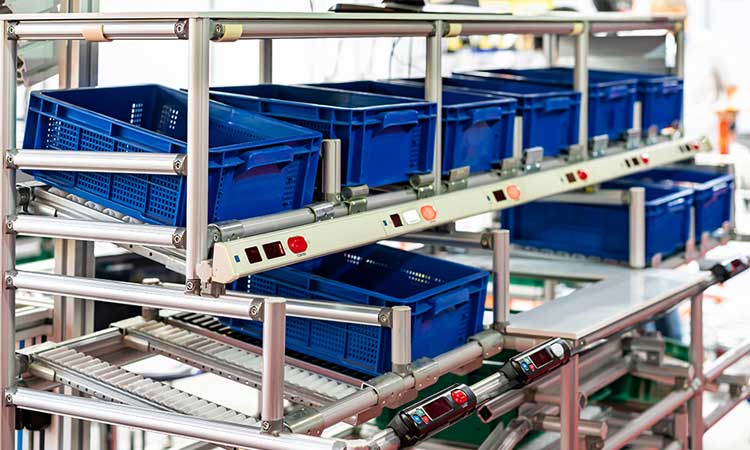
Optimizing Operations for a Pharmaceutical Distribution Center
Background: A pharmaceutical distribution center (DC) utilizes various storage systems: A-frames for frequently demanded prescription and OTC drugs, gravity flow racks for less demanded items, and static racks for slow-moving items. During the day, these systems are restocked while orders from hospitals and pharmacies are placed. At night, orders are picked, assembled, sorted, and checked. By dawn, delivery trucks depart the DC to deliver the orders to customers.
The Challenge: The addition of a major pharmacy client has introduced several logistical challenges:
1. Meeting Target Departure Times: Trucks are consistently leaving the DC later than their scheduled departure times.
2. Reducing Overtime Costs: Overtime costs are increasingly above target levels.
3. Managing Emergency Restocks: Emergency restocks are becoming more frequent.
Key Considerations: 1. Optimize Product Placement: Evaluate which products and in what quantities should be placed on the A-frames to ensure high-demand items are easily accessible. 2. Seasonal Stocking Levels: Plan stocking levels and locations based on seasonal demand (e.g., flu season or allergy season) to ensure adequate supply and reduce emergency restocks. 3. Flexible Labor Policy: Implement a flexible labor policy to shift pickers across zones based on nightly picking demand, ensuring efficient use of labor and reducing overtime costs.
By addressing these considerations, the DC can improve its operational efficiency, meet target departure times, and reduce overtime labor costs.
Queuing
Managing Warehouse Inbound Shipments with Limited Docking Space
A retail distribution center operates a large warehouse that receives frequent inbound shipments from various suppliers. The warehouse has a limited number of docks (loading bays) where trucks can unload their shipments. Each shipment may arrive at different times throughout the day, and the unloading process takes a certain amount of time depending on the size of the shipment.
The challenge is to minimize delays, optimize the use of docking space, and ensure that shipments are unloaded and processed efficiently. The warehouse needs to deal with queues of trucks waiting for available docks to unload, especially during peak times.
This type of queueing problem is common in warehouse management and port logistics, where unloading docks are limited but there is a constant flow of shipments that need to be processed efficiently. Companies like Amazon, Walmart, and FedEx use queueing models to optimize their warehouse operations and delivery systems, ensuring that they can meet demand without excessive delays.
For example, ports like those in Los Angeles or Hong Kong, where large numbers of ships arrive to unload cargo, must manage limited docking space and ensure that trucks or cranes are efficiently used to unload goods without long queues of trucks waiting to be serviced. Similarly, distribution centers that receive inbound deliveries from suppliers have to optimize dock usage to minimize waiting time and ensure on-time deliveries to retail stores.
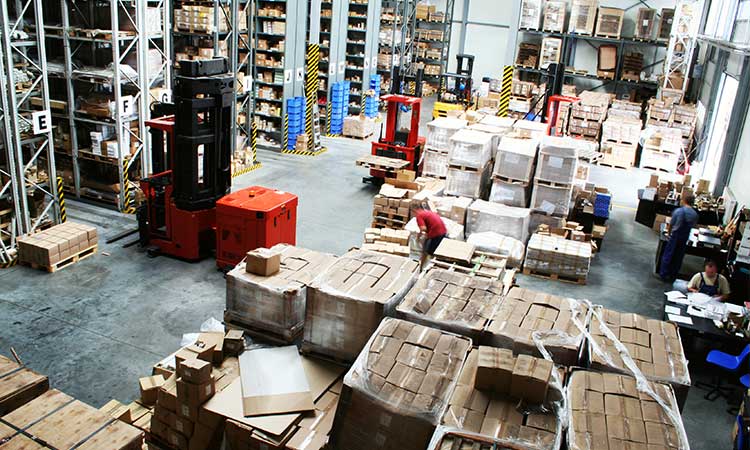
Routing
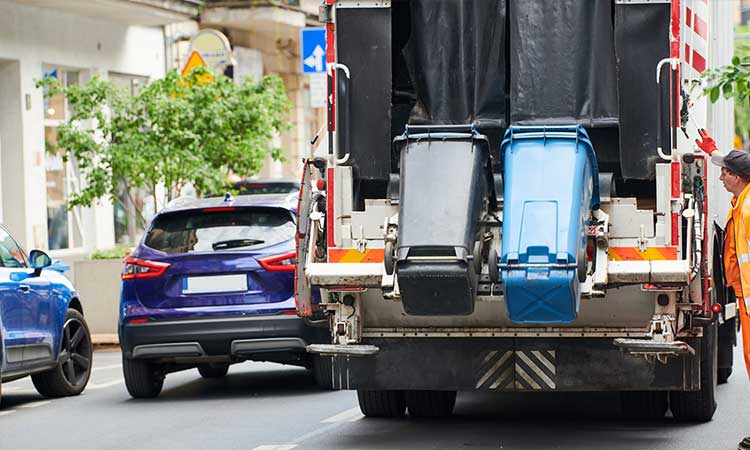
Optimizing Trash Collection Routes for a Metro Atlanta Neighborhood
Background: A refuse company has a service contract for trash collection in a large subdivision in metro Atlanta, consisting of approximately 4,000 homes. The streets are a mix of one- and two-way, and trash pickup occurs once weekly, every Tuesday.
The Challenge: The company currently uses three trucks to service the subdivision. All trucks enter at a fixed point (x) and exit at a different point (y) after completing their routes. While no single truck or pair of trucks has enough capacity to service the entire neighborhood, the combined capacity of all three trucks is sufficient. Therefore, all three trucks must be utilized in some configuration.
Key Objectives:
1. Minimize Combined Travel Distance: Develop fixed routes for each truck to ensure the least combined travel distance for all three trucks.
2. Adhere to Capacity Limits: Ensure that no vehicle exceeds its capacity.
3. Complete Coverage: Ensure that each street is traversed at least once, adhering to the direction of one-way streets where necessary.
By optimizing the routes with these objectives in mind, the company can improve efficiency and reduce operational costs while ensuring reliable service for the neighborhood.
Below are examples of supply chain and logistics related student projects addressed as part of the Georgia Tech School of Industrial and Systems Engineering Senior Design program.